Most homeowners want the best for their money. Whether it’s the best car, computer, or foundation repair method, you want the most value for your investment.
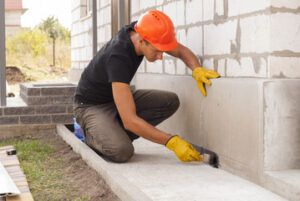
Foundation repairs require professional expertise to be effective. While DIY fixes may seem cheaper, they can be unsafe and ineffective for the long term. Visit https://www.apexplanofoundationrepair.com/ to learn more.
If you see cracks in your walls or a sinking foundation, it’s critical to contact a professional for inspection and repairs. Ignoring the problem will only allow it to exacerbate, potentially leading to serious structural damage and expensive repair bills down the road. A good foundation repair company will not only fix your existing problems but prevent future issues from arising as well, saving you money and anxiety in the long run.
Even minor issues like sticking doors and windows can indicate more serious problems if left unaddressed. Foundation problems can also affect your home’s functionality, making it difficult to lock doors or keep pests and moisture out. A professional will recommend a variety of methods to address the issue and prevent it from becoming worse, such as piering or slab jacking.
These methods involve digging and drilling into the soil around your home to install steel or concrete piers that extend down through unstable layers to support the foundation. The process may take a few days to a few weeks, depending on how many piers are needed and how much of the house is affected. In about 10% of cases, supports are required under the middle of the house as well, a process known as underpinning.
Once the piers are installed, your foundation will be lifted to its original position. This is especially useful for homes that have experienced significant settling, as it restores stability and eliminates the need for costly excavation. Another preventive method is waterproofing, which involves adding a barrier to your basement or crawl space to protect it from moisture.
Poor drainage is often the root of foundation problems, causing the soil to expand and contract, which can lead to cracks in the foundation and other areas of your home. A foundation repair specialist will recommend methods for addressing drainage issues, such as installing gutter systems and drainage trenches to divert water away from the home. They can also advise you on the best landscaping for your home, which will help to prevent soil movement by keeping plants and roots away from your foundation.
Preserving Your Home’s Value
A well-maintained foundation can protect and enhance your home’s overall quality, resulting in increased property value. In contrast, a neglected foundation can impact the structural integrity of the entire structure and negatively affect its appearance. Fortunately, addressing problems before they worsen can prevent lasting damage and save you time, money, and stress in the long run.
Whether you’re planning on selling your home in the future or are simply interested in maintaining its value, foundation repair is an essential investment. The foundation is the backbone of the home, and when it’s damaged, other parts of the house will feel the impact and show the disrepair. A strong, stable foundation can make the house more appealing to buyers and reduce the risk of costly repairs after the sale.
If you choose to hire a contractor for foundation repairs, be sure they have the experience necessary to provide a high-quality service and ensure your safety. You should also research local contractors to determine their licenses, insurance policies, and customer reviews. Additionally, contractors that specialize in your area’s soil conditions and climate are likely to have a better understanding of how to solve specific issues.
Once you’ve hired a professional, they can create a repair plan that pinpoints where the supports need to be placed. In most cases, these supports will be needed along the perimeter of the house where the foundation has settled or sunk. In about 10% of cases, however, support may be needed under the middle of the home as well. The two most common methods for installing these supports in Central Texas are piers and pilings. Piers are constructed by digging and drilling into the ground to create steel or concrete piers that extend below the foundation and stabilize it. They are an effective solution for homes built on expansive or shifting soils. Pilings are a more cost-effective method that involves pressing steel or concrete pilings into the ground until they reach stable soil layers. They are ideal for newer homes or those that have recently undergone a remodel to avoid damaging new finishes and structures.
Preventing Health Issues
If left unaddressed, foundation issues can escalate into significant problems that affect the structure of your home and put your family’s safety at risk. These problems include:
Cracks in walls, especially those that are widening over time. Uneven floors, sagging ceilings, and doors that stick or won’t close properly due to shifting foundations. Visible gaps around windows and doors that have appeared suddenly. These signs indicate that the foundation is failing to support certain parts of your home, which can result in structural damage and a dangerous living situation.
Moisture promotes the growth of mold and mildew, which can wreak havoc on the building materials in your home. This moisture can deteriorate wood beams and joists, making them weak and unsafe to use. In addition, it can lead to rotting and water leaks. Moisture can also create the conditions for the growth of termites, a serious pest that can eat through the wooden beams and joists in your home’s foundation and cause further damage.
A professional company can perform a variety of different methods for foundation repair, depending on the severity of the issue. One of the most common techniques is steel piers, which involve driving long, slender steel rods deep into the ground to provide a stable base for your home’s foundation.
When choosing a contractor for foundation repair, consider their experience and the types of repairs they’ve successfully handled in the past. Make sure they are licensed and insured, as well. A contractor with experience in the local area will have a better understanding of soil and climate conditions and may offer more effective solutions than someone who has little knowledge of your region’s unique challenges.
Regular inspections can help catch minor issues early and prevent them from getting worse. Be sure to check your home regularly for any new cracks, water in the basement, or changes in the way your doors and windows work. A quick response to these issues can save you a lot of money and headaches in the future. If you notice any of these issues, contact a foundation repair company right away to schedule an appointment.
Preserving Your Family’s Safety
In addition to cracks in the walls, foundation damage can lead to uneven or bouncing floors that create tripping hazards and misalign doors and windows. If you notice these problems, they should be addressed quickly to prevent further damage and keep your family safe.
A qualified professional can identify and address any issues with your home’s structural integrity before they worsen. Using methods like helical piers and pressure grouting, they can stabilize your building’s foundation. This keeps it in place and ensures that any other parts of your home are functioning correctly.
This service is a cost-effective way to protect your investment, save on future repair costs and keep your home’s value up. It’s important to choose a professional with experience and a good reputation. Look for testimonials and reviews that indicate they can meet your needs and provide lasting solutions.
A good foundation repair company will also offer other services that can help you maintain your home’s safety and stability. They may install a drainage system to prevent water from pooling around your foundation, and they can recommend landscaping changes that direct water away from your house. They can also help you make sure your crawl space or basement has proper humidity levels to prevent mold growth and wood rot.
Foundation damage can be costly if you let it get out of hand. The longer you wait to seek repairs, the more expensive and complicated it will be to fix the problem. By responding to small problems as soon as they appear, you can reduce the impact on your budget and avoid major structural damage in the future.
When looking for a foundation repair service, consider the benefits of hiring a local contractor. Choosing one with experience and a good reputation will help ensure that your foundation is repaired in a timely manner and that the problem won’t recur. Licensed and insured contractors can also guarantee their work, giving you peace of mind. They’ll know the conditions in your area and can customize their repair techniques to suit them. They can also offer a warranty on their services, so you can feel confident that your foundation is fixed for good.